The DurAnode System
DurAnode – Tube Anode for embedding inside elements
a) durAnodes have a built in pre-resistor which eliminates IR drop problems and uneven current distribution and allows long anode strings to be developed.
b) durAnode has a unique anode connection system that has been developed to accommodate up to 3 wires and requires no soldering but allows highly reliable connections.
c) A complete range of control systems have been developed specifically for use with durAnodes.
d) The durAnode system uses an acid resistant backfill grout to provide the ionically conductive connection between the MMO mesh anode and the parent concrete. This is tolerant to the acid build up that occurs with all CP systems and have led to failures when using alkali grouts/mortars.
DurAnodes are designed to be installed in walls, decks and soffits. They are a perfect replacement for undeveloped tube anodes because they require only small diameter holes which reduces noise and damage to the structure. They also have several built in features that overcome the installation problems of standard tube anodes.
The anode consists of three parts: the durAnode4 anode assembly, a cementituous backfill compound and a special connecting wire. The anode assembly has an anode tube which is made of an inert coating applied to a titanium mesh with a central insulating body and a head where the connection to the special wire is made. This central body has a resistor. The backfill compound consists of a cementitious grout which functions as an ionic conductor between the anode tube and the electrolyte, i.e. the concrete, stone or brick. The connecting wire is attached to the anodes. The wire can be hidden in a slot between the individual anodes
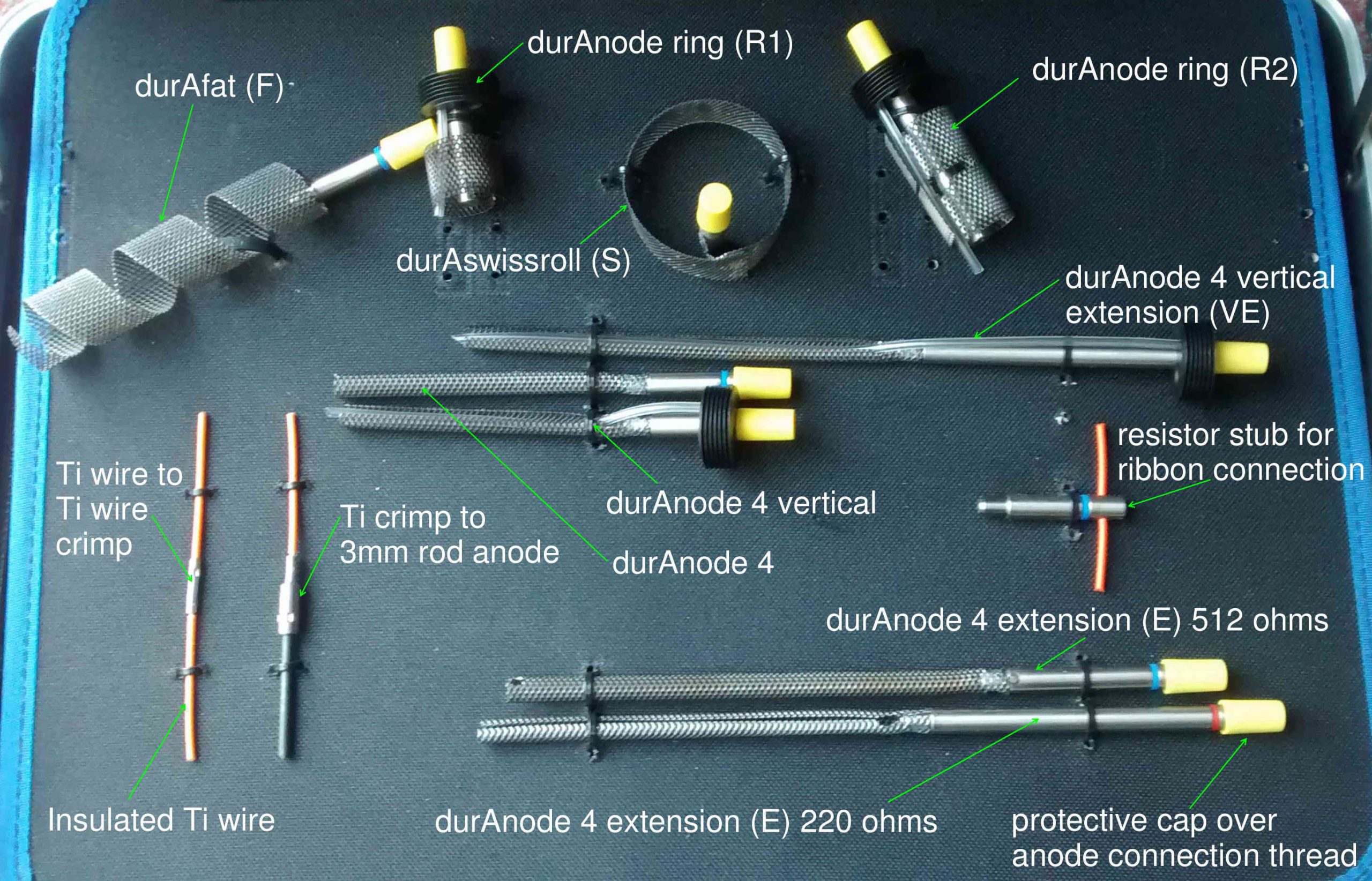
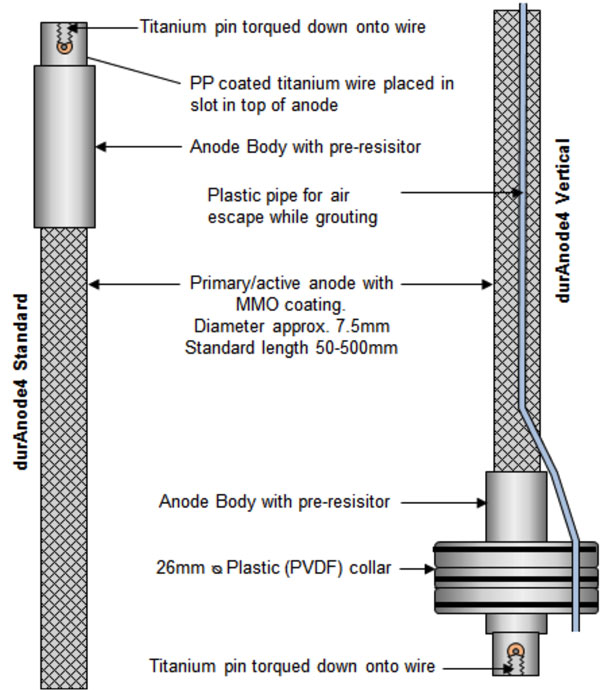
To install a durAnode4 a hole is drilled into the concrete or masonry of sufficient length to accommodate the anode rod, body and head as detailed in the design. The hole must not be in direct contact with the rebar as otherwise a short circuit will result. In order to prevent this occurring a special covermeter has been developed named the durAbar, which is placed in the drilled hole before the anode or backfill and gives a readout on the suitability of the hole for use.
Two different types of durAnode4 are available for use of different installation angles. In the special case of ‘horizontal’ anodes which are exposed to water (i.e. at tide level) the durAnode4 vertical should be used. durAnode4 (standard) is used when the hole is pointing downwards (10 degrees or more). durAnode4 vertical is used in holes pointing upwards (5 degrees or more). Care should be taken to prevent water coming into the anode hole before and after casting the anode.
The specially designed torque pin bites into the titanium wire to ensure a simple and repeatable connection that is highly durable as the titanium wire is not exposed.
The maximum continuous recommended durAnode output in wet and salty concrete is 500mA/m2 of anode area in the proprietary grout. Ongoing independent long-term tests (currently over 16 years) on a commercial structure have shown that there is no backfill or anode deterioration at this maximum recommended current density.
The durAnode pre-resistor is unique to durAnode and provides a major advantage over other anodes in that it minimises non-uniform current density. Combined with the proprietary acid resistant grout this eliminates the acidification issues and over driving of the titanium anode. This is shown for current out puts in concrete of different resistivity below.
Current Output At Various Resistivities
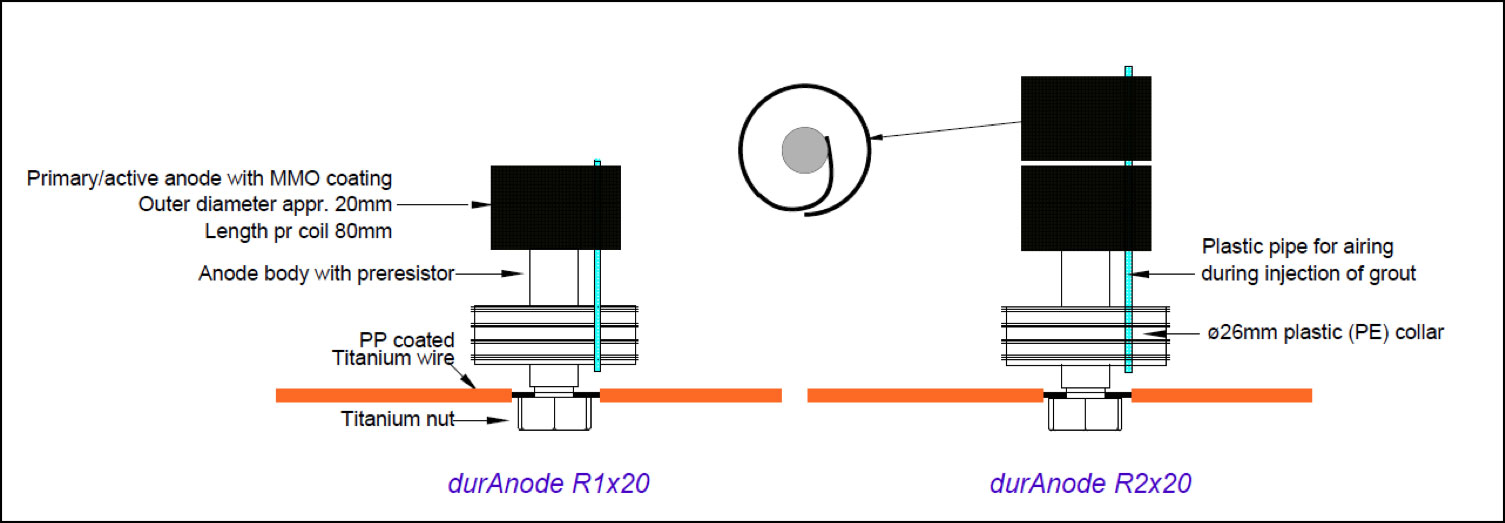
References
Chess. P., Crevello. G., Noyce. G., “Anode Performance: The Use of Ballasted Mix Metal Oxide Coated Titanium Anodes in Impressed Current Systems installed within Historic Steel Frame Masonry Clad Structures.
ABSTRACT: Corrosion damages in historic steel frame structures have a great physical and financial impact on the performance and treatment of the building façade. Minor cracking and displacement of masonry can eventually lead to spalling and loss of stones and, as seen in rare instances, the loss of life if large masonry units become dislodge and fall from great heights due to corroding steel supports.
Cathodic Protection is a corrosion mitigation technique, which minimizes stripping of the masonry while simultaneously protecting the steel from corroding. The core philosophy for the use of Impressed Current Cathodic Protection (ICCP) in historic buildings is to protect cultural heritage from the ravages of corrosion and the designer’s scope is meant to follow conservation guidelines. This approach anticipates that no additional harm will be incurred by a building upon or after installation of a system. For this reason, the appropriate an-ode must be utilized within the parameters of the structure.
It is critical that electrochemical reactions be minimized at the surface of the masonry. The reaction can have dire consequences on historic masonry, not only deteriorating the mortar, but dissolving limestone or cast stone in the correct circumstances. The designers’ role is to recommend the best anode system for the subject building.
The use of ballast anodes within these circumstances have led to better overall performance of ICCP Systems in Historic Steel Frame Structures. The paper will look at two case studies where different ballast anodes types were installed within historic steel frame structures, and discuss the benefits of the Ballast resistors.
Case Studies will review long term monitoring data, photographic records from past installations and will review the installation process of installing the ballast resistors in historic steel frame construction and why the anodes were chosen and how they have performed since energization.